Description of the problem
Waste management is one of the most emerging issues for food processors. The industrialized production of egg products in Europe (e.g. in powder, liquid and frozen form) offers a series of economic benefits. However, the egg processing industry generates a large amount of waste, mainly eggshell (about 11% of the total egg weight).
150,000 tons/year of eggshells are generated at European level in egg-producing companies. The two countries involved in this project are producing 5,400 tons/year (Portugal) and 16,000 tons/year (Spain), with associated transport and treatment or landfill costs of up to 25 to 60 euros/ton. This can result in costs in the order of 50,000 to 100,000 euros/year in the case of medium-sized ovo-producing companies.
Eggshells are mostly composed of calcium carbonate (95% of the shell weight), magnesium carbonate (1%), calcium phosphate (1%) and water. Therefore, once the membrane is separated, they can become an alternative source of calcium carbonate. Although this is not its most common use, large quantities of calcium carbonate are used in the manufacturing of ceramic tiles.
Considering the principles of circular economy, the transformation of a waste such as eggshell into a bio-based raw material and the need to reduce the consumption of virgin raw material, this project aims to demonstrate the feasibility of using eggshell as a secondary raw material in the manufacturing of tiles.
This valorization scheme does not alter the constituent of the membrane. Therefore, this small part of the waste (less than 5% of the total weight) can continue to be landfilled as today or -considering that only the organic part will be involved- new uses could be looked into by the ovo-producing industries.
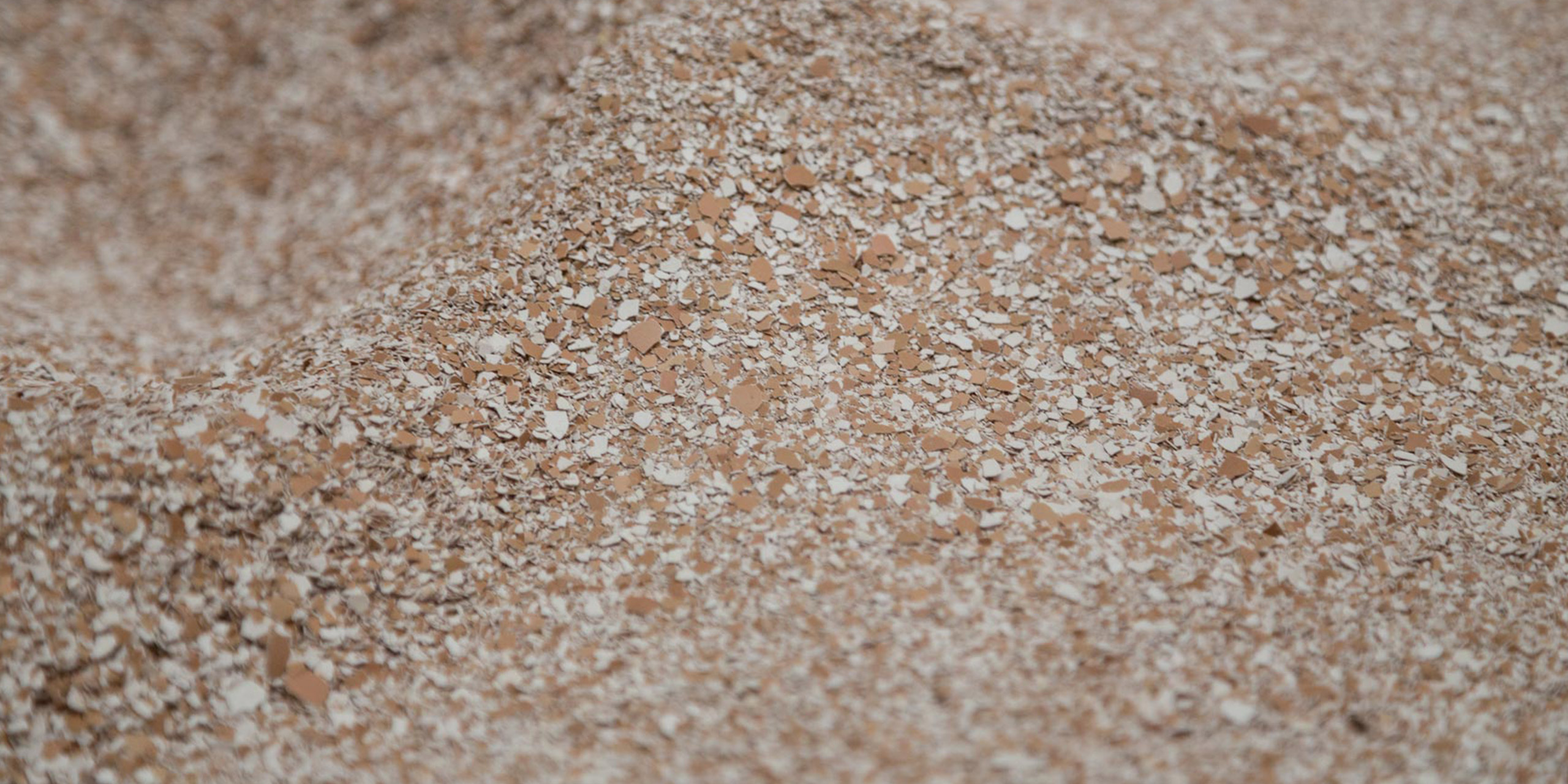
Prototype
The prototype is key to the success of the project. It must allow for the separation of the membrane in such a way that the resulting bio-carbonate has zero or practically zero organic matter content. This prototype will be built by the machinery manufacturer MAINCER and will be installed in the ovo-producing company AGOTZAINA for validation and later obtaining of the bio-CaCO3 for the manufacturing of tiles in industrial tests.
The prototype will consist of the following elements:
- Sieving separation system to eliminate most of the membrane.
- Crushing system to eliminate the small fraction of residual membrane.
This video shows the initial design of the prototype:
The completion of the industrial tests will allow for the validation of the developed prototype, becoming a suitable and reference solution for the disposal of eggshell waste generated by egg-producing companies.
Validation of the proposed solution
Industrial tests to be carried out between September 2022 and June 2023 will demonstrate this solution, producing at least 4,000sqm of tiles with percentages of bio-carbonate ranging between 5 and 12%.
The feasibility of this solution stems from the fact that the European ceramic industry has a high consumption of calcium carbonate. This industry is a world leader in the production of high quality ceramic tiles, representing more than 10% of world production. Spain and Italy are the largest producers in the EU. Tiles are the type of ceramic tile used for wall cladding and account for more than 25% of the total volume of ceramic tiles manufactured. They consume large quantities of calcium carbonate, between 10 and 15% by weight, together with clays and sands. According to the production of ceramic tiles and taking into account these percentages, the ceramic sector consumes 300,000 tons of calcium carbonate annually at European level (of which 150,000 tons correspond to Spanish ceramic companies and 30,000 tons to Portuguese companies). Considering these data and the fact that -through the separation process designed in Life EggshellenCE- approximately 85% of eggshells can be transformed into calcium bio carbonate, the ceramic industry could absorb in both countries and at European level the totality of eggshells produced by egg-producing companies.
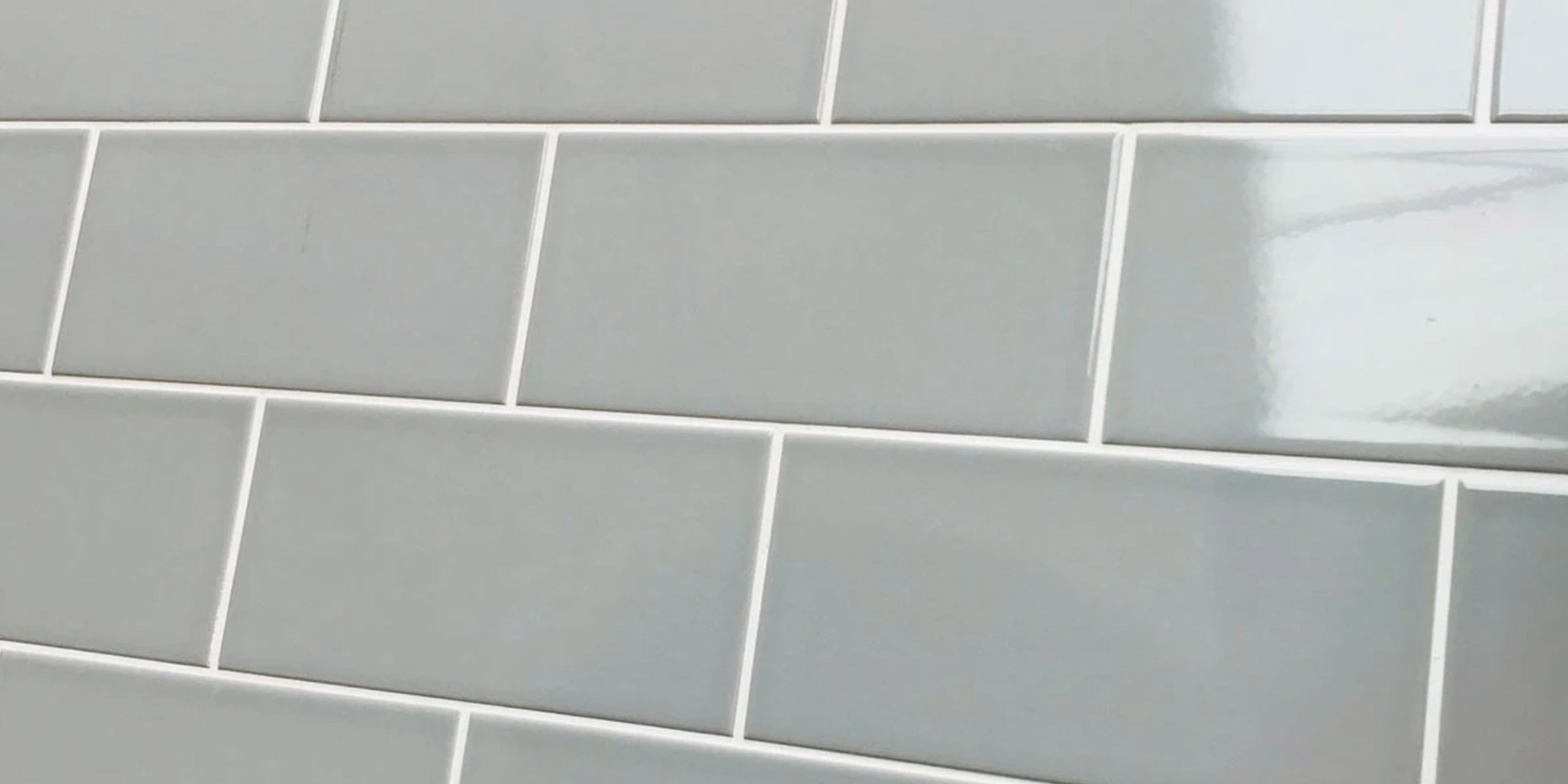
Execution
Development of the prototype is scheduled to begin in October 2020 with completion in February 2022.
Once developed, industrial tests will be performed in order to evaluate and validate the solution.
Fine-tuning of the equipment
The sketch of the machines to be manufactured in the future, designed by Maincer to separate and extract the biocarbonate from the eggshell, is already available.